A gear-type aging tester (forced-circulation heat aging tester) evaluates the heat aging properties of high polymer materials such as plastics and rubber by heating a test specimen to accelerate aging in the materials. Heat exposure is a primary cause of deterioration in high polymer materials. However, many electronics such as televisions and computers and mechanical products such as vehicles generate heat during operation. Deterioration caused by heat can jeopardize product safety. Therefore, it is necessary to evaluate the heat aging stability of each material.
Test Overview
The test specimen is suspended in a chamber set at the test temperature and then exposed to heat for a specified period to accelerate deterioration. The specimen is then visually evaluated and its physical properties are measured (such as via tension tests) to evaluate its heat-aging stability.
Testers
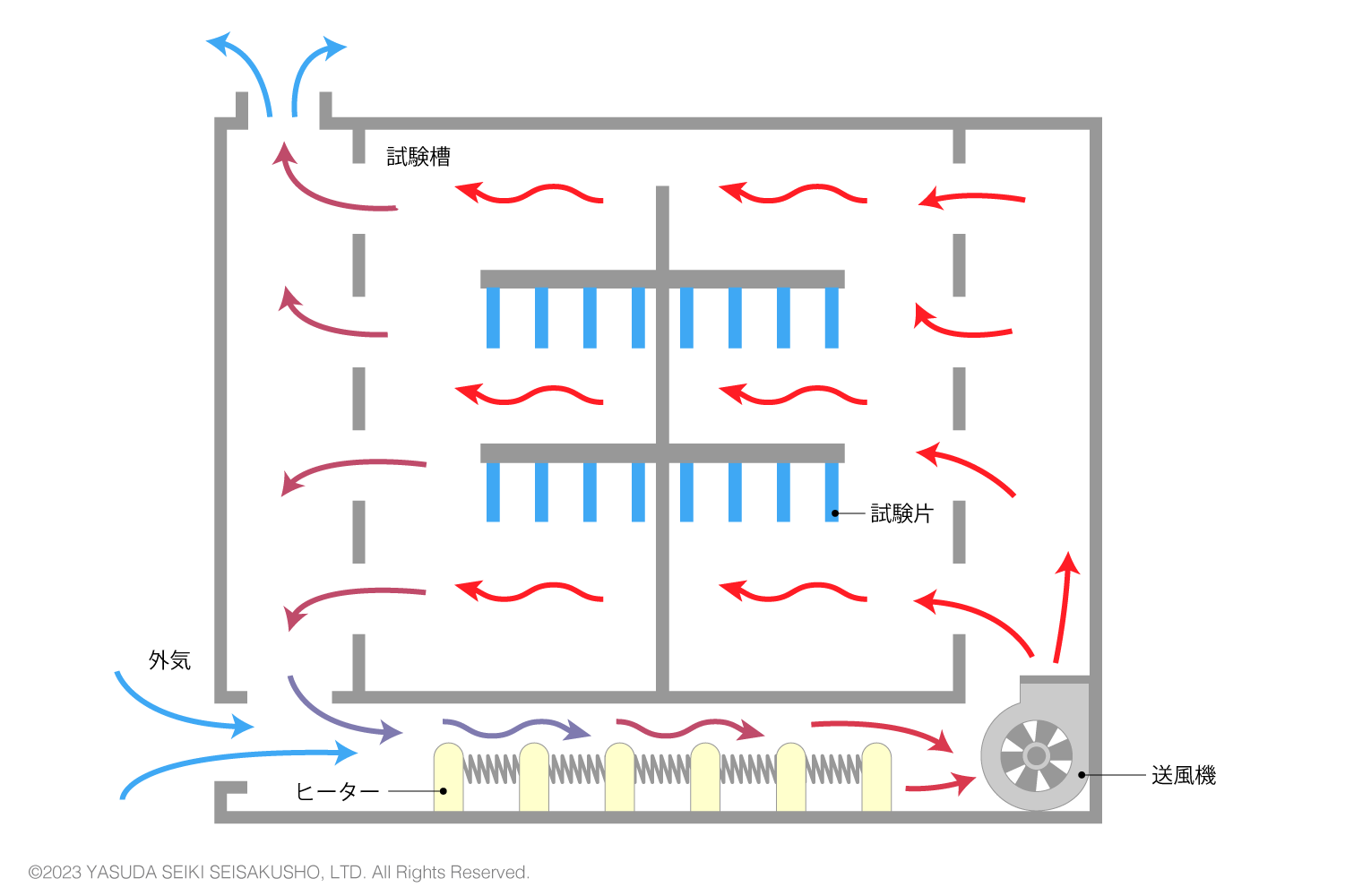
The tester uses a “forced-circulation type” heating chamber that forcibly circulates the air inside the test chamber. The tester consists of a test chamber, a circulation device, an air substitution device, a temperature control device, and a test specimen installation device.
Test chamber
The test chamber is equipped with an internal test specimen mounting frame (or a rack) that does not impede the circulation of hot air, and includes a structure that uses thermal insulators to keep the test chamber warm and block outside air.Test specimen mounting frame
A single-shaft rotating frame that rotates 5 to 10 times per minute.
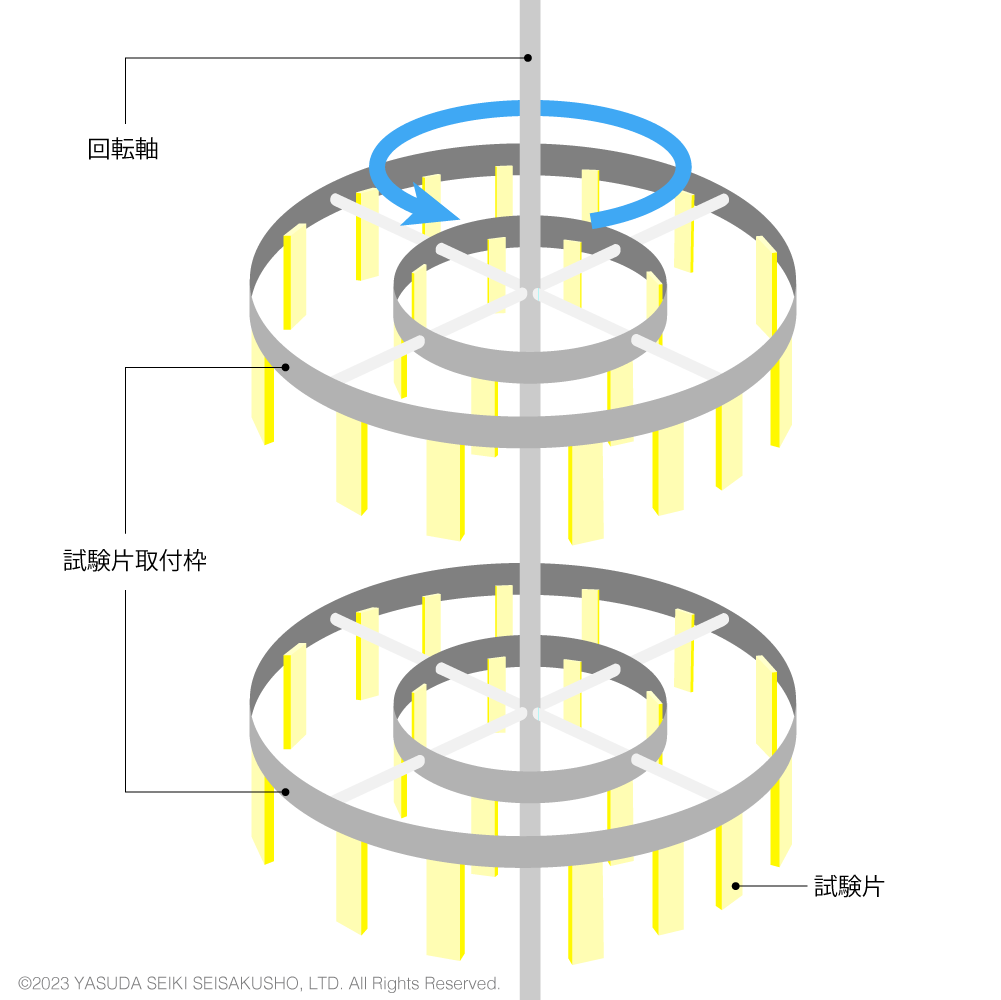
Performance
Each standard is defined as given below.
Standard | B 7757 | K 6257 | K 7212 | ||||
---|---|---|---|---|---|---|---|
Model | Type I | Type II | Type III | Crosswind type | Range wind type | A type | B type |
Type | JIS type | UL type | – | – | – | – | |
Air Change Rate (Times/hour) | 3 to 10 | 5 to 20 | 100 to 200 | 3 to 10 | 3 to 10 | 1 time per minute or more | 3 to 10 |
Average wind speed (m/s) | 0.5±0.1 | – | – | 0.5±0.1 | 0.5 to 1.5 | 1±0.2 | 0.5±0.1 |
Time constant | – | 660 or less | 660 or less | – | – | – | – |
Specific heat (J/g-K) | 1.003 | 1.003 | 1.003 | 1.006 | 1.006 | 1.003 | 1.003 |
Temperature settings range | Ambient temperature + 20°C and 300°C | – | – | – | Ambient temperature + 20°C to 300°C | ||
Temperature control accuracy | Set temperature ±1°C | – | – | Up to 100°C:±1°C 125 to 300°C:±2°C |
Set temperature ±1°C |
Temperature Distribution
Temperature distribution is expressed as the difference between the maximum and minimum temperatures at nine locations specified in the standard.
The distribution will be as given below according to the temperature setting range.
Test temperature T (°C) | Temperature distribution (°C) |
---|---|
T ≦ 100 | 2 or less |
100 < T ≦ 200 | 4 or less |
200 < T ≦ 300 | 6 or less |
Measurement Method
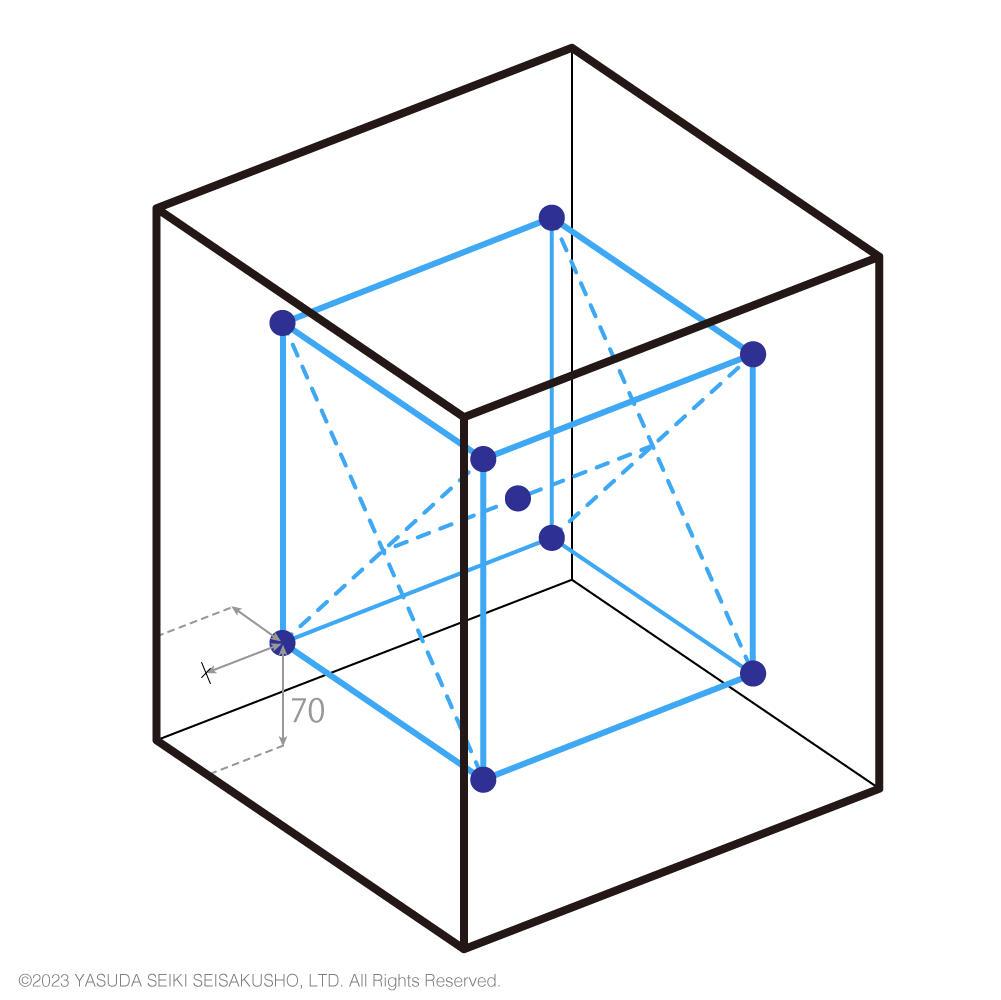
The temperature distribution is measured at eight vertices of a cube formed by planes located 70 mm inside from each wall of the test chamber, and at one additional location at the center of the test chamber, making a total of nine locations. After the temperature is sufficiently stable, the temperature is measured at the nine locations for 24 hours, and the difference between the highest and lowest temperatures is derived. Fluctuations in the ambient temperature over a period of 24 hours must be ±10°C or less of the set temperature and within ±5% of the set temperature.
*Many simple “ovens” do not meet this standard. Proceed with caution if you wish to implement the test according to the standards.
Test Conditions
Test conditions depend on the test specimen used in the test.
Furthermore, each standard is as described below.
K 6257 (Rubber)
Depends on the type of rubber. Select from the time and temperature specified in K 6250.K 7212 (Plastics)
Temperature at which the specimen ages for the appropriate test period
*The test time is not clearly specified.
Test Type (K 6257 Rubber)
There are two types of tests: Accelerated aging test (At method) and Heat resistance test (Hr method).
Accelerated Aging Test
In this test, the specimen is tested under higher temperatures than the actual usage conditions to recreate the effects of natural aging in a short period.Heat Resistance Test
In this test, the specimen is tested under temperatures similar to that at which the specimen will be exposed under actual usage conditions.
Evaluation Method
For Rubber
The physical properties of the test specimen are measured after the aging process is complete. Then, the change from the pre-aging value is calculated to examine the heat-aging characteristics.
The rate of change in the physical properties other than hardness is calculated by using the following formula.
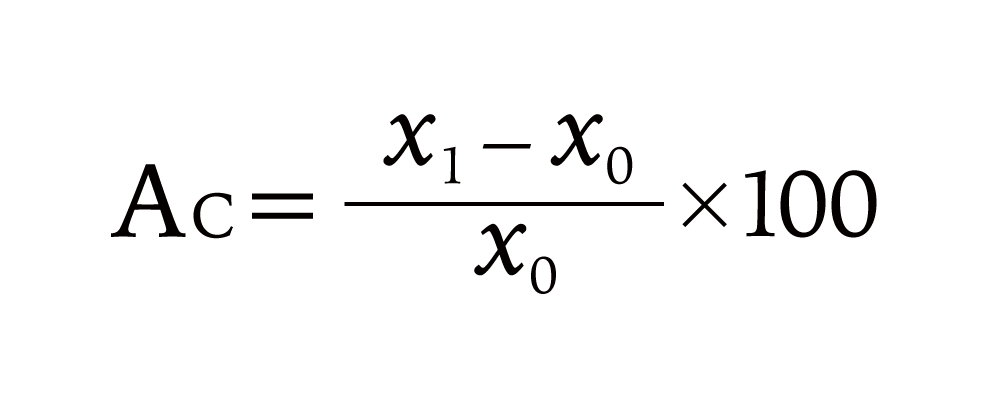
Hardness is calculated by using the following formula.
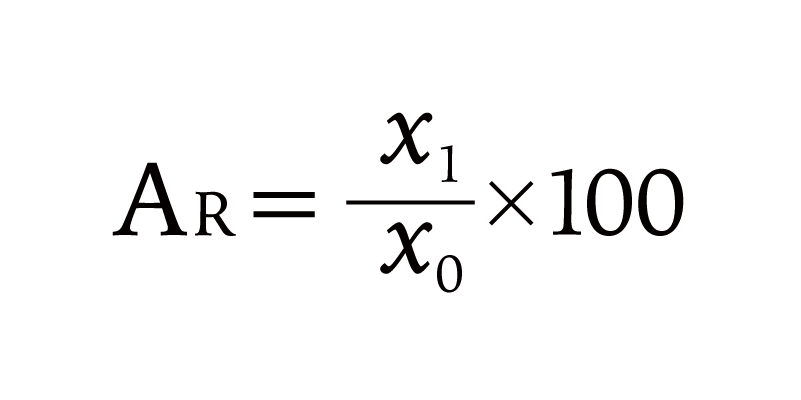
AC: Rate of change after aging with regards to the physical properties before aging
AR: Retention rate after aging with regards to the physical properties before aging
X0: Median physical properties before aging
X1: Median physical properties before aging
The retention rate is calculated by using the following formula.

AH: Change in hardness
H0: Median hardness before aging
H1: Median hardness after aging
AC: Rate of change after aging with regards to the physical properties before aging
AR: Retention rate after aging with regards to the physical properties before aging
X0: Median physical properties before aging
X1: Median physical properties before aging
AH: Change in hardness
H0: Median hardness before aging
H1: Median hardness after aging
For Plastics
JIS K 7212 states that results are judged “based on the degree of change in the properties of the test specimen after a specified period, or the time it takes for the properties to reach the specified value.”
The criteria to determine aging depends on the concerned parties; however, the criteria to determine aging is often evaluated with the following methods.
- Visual observation (instances such as powder formation, cracks, and deformation on the test specimen)
- Change in mass
- Decreased performance in tension tests, bending tests, etc.
- Decreased optical performance such as fading
- Decreased electric resistance performance such as dielectric strength and insulation resistance
Air Change Rate
The air change rate indicates the number of times air is replaced per hour and is determined by the airflow rate into the test chamber and the capacity of the test chamber. The airflow can be measured indirectly by the “power consumption method” and directly by the “flowmeter method.” The commonly used “power consumption method” is explained below.
Power Consumption Method
The difference between “the amount of electricity required to close the air inlet/outlet and maintain the chamber at a specified temperature” and “the amount of electricity required to maintain the same temperature when the air inlet/outlet is opened” can be measured in the power consumption method to calculate the amount of changed air.
[Measurement Method]
- Close the inlet, the exhaust vent, and the safety cover, and seal the gaps with an adhesive tape. Completely block off the air inside the test chamber from the outside.
- Start the fan and raise the ambient temperature inside the chamber to +80±2°C
- Measure the power consumption for at least 30 minutes after the temperature stabilizes (after approximately 3 hours)
- Open the inlet and the exhaust vent, and calculate the power consumption during ventilation
The air change rate is calculated with the following formula.
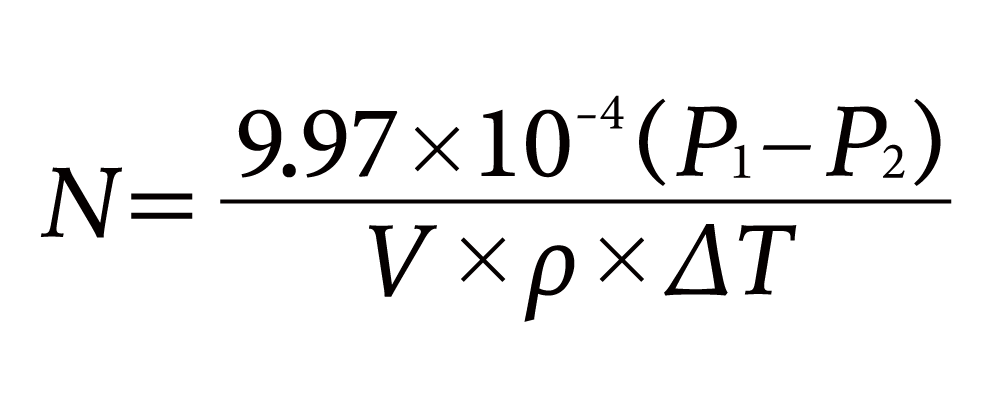
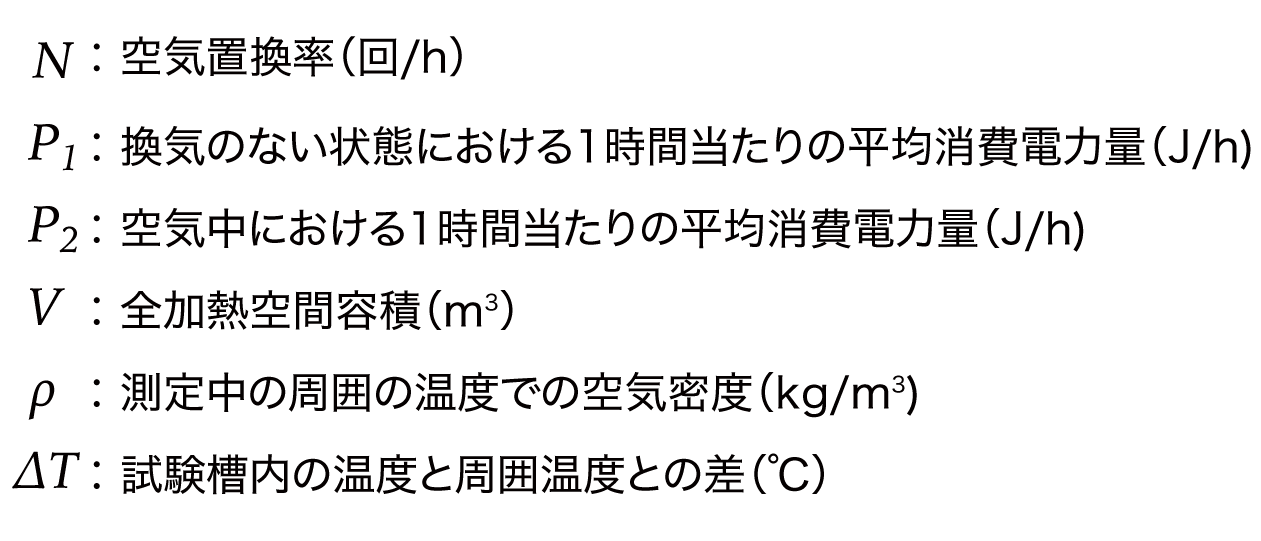
However, in the case of JIS K 6257, the rate is calculated by using the following formula.
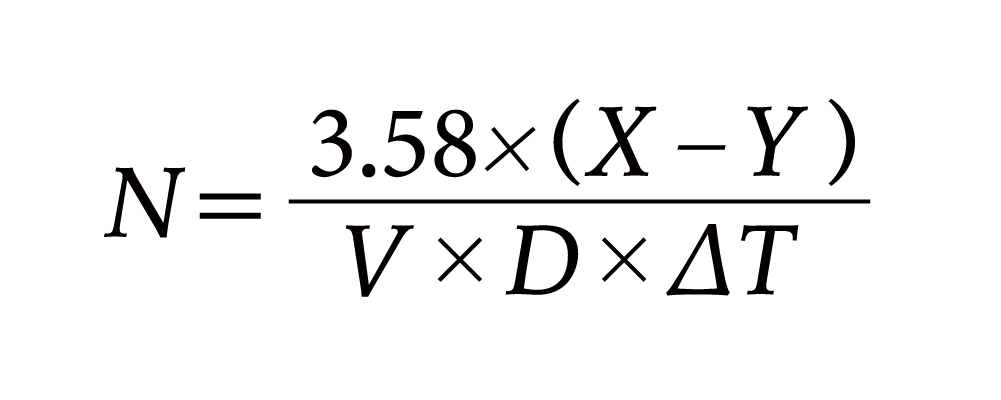
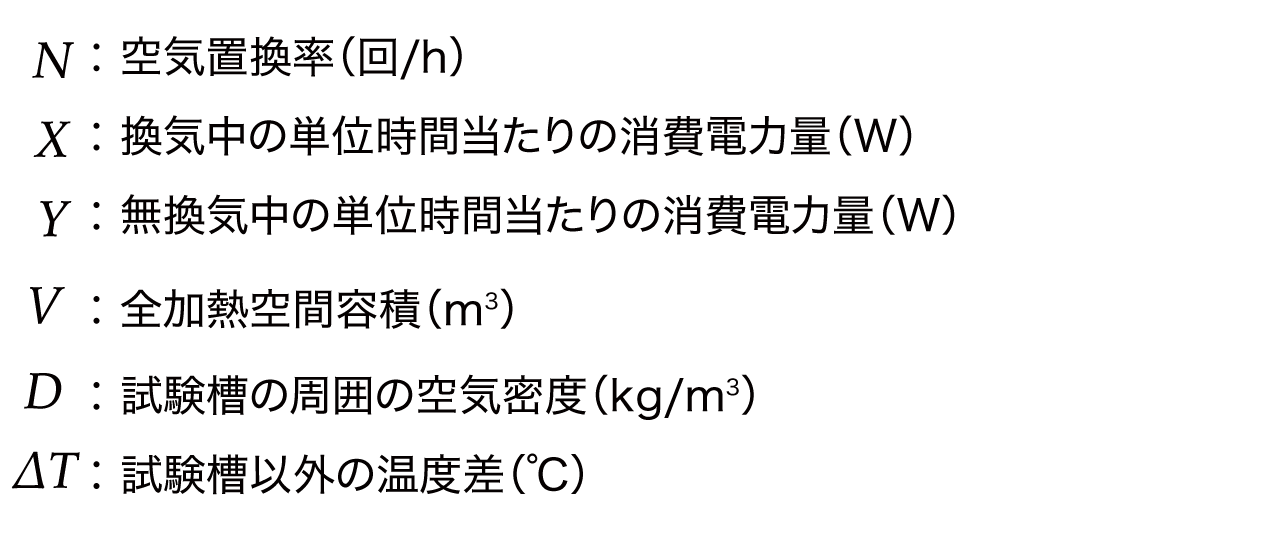
The formulas for calculating the air change rate are different for the plastic standard (K 7212) and the rubber standard (K 6257) as these standards use different units for specific heat at constant pressure and power consumption.
What is UL Standard?
UL746B is a UL standard for long-term heat resistance. The heat resistance of plastics when exposed to high temperatures for long periods of time is called “long-term heat resistance.” Aging and deterioration due to heat cause the physical properties of plastics to degrade. The Relative Thermal Index (RTI) of UL746B is often used as an indicator of long-term heat resistance, and the tensile strength, impact strength, and electrical insulation properties are evaluated after exposure to high-temperature environments for long periods of time.
An indicator of a material’s ability to maintain certain properties (physical, electrical, etc.) when exposed to high temperatures for long periods of time. It also serves as a measure of thermal durability. This refers to the temperature at which the initial physical properties of plastic deteriorate by 50% or less when exposed to air for a specified period of time.
*Our No.102 Gear Aging Tester complies with this standard.
Details of the Standard
It is stated in UL746B that the test method must comply with ASTM5374-93 and the equipment must comply with the standard specifications of ASTM 5423-93 Type 1.
[Air Change Rate]
The notation for air change rate in each standard is as follows.
-
◆ ASTM5423-93
At 100°C or the maximum operating temperature, Type 1 ovens need to be set at 5 to 20 times/h, and Type 2 ovens need to be set at 100 to 200 times/h. -
◆ ASTM5374-93
Measure the air change rate at the maximum operating temperature of 100±2°C.
Usually, tests are conducted at four temperature points. The temperature is set such that the endpoint* is at least 500 hours at the highest temperature, and at least 5000 hours at the lowest temperature. The RTI is calculated based on the test results.
*Endpoint: Time when the physical properties degrade by 50% or less
There is an indicator called a short-term heat resistance in contrast to long-term heat resistance. The long-term heat resistance refers to long-term stability of a physical property that indicates when no external force is applied to the plastics, whereas short-term heat resistance refers to the temperature at which deformation and breakdown occur in a high-temperature environment and when a load such as weight is applied to the plastics.
*Heat deflection temperature (HDT) can be used as a reference. See Yasuda Seiki’s No.148-HD Heat Distortion Tester page for short-term heat resistance evaluation.
Standard List
Standards for heat aging tests are provided in both JIS (ISO) and ASTM and test methods have been standardized in each standard, respectively.
Standard | Year | Applicable to | Standard name | |
---|---|---|---|---|
JIS | B 7757 | 1955 | Testers | Forced circulation type air heating aging tester |
K 6257 | 2017 | Rubber | Vulcanized rubber and thermoplastic rubber – Method to determine heat aging properties | |
K 7212 | 1999 | Plastic | Plastics – Thermal stability test method for thermoplastics – Oven method | |
C 3005 | 2014 | Electric wire | Rubber/plastic insulated wire test method | |
ISO | 188 | 2023 | Rubber | Rubber, vulcanized or thermoplastic – Accelerated ageing and heat resistance tests |
4577 | 2019 | Plastic | Plastics – Polypropylene and propylene – copolymers – Determination of thermal oxidative stability in air – Oven method |
|
ASTM | E145 | 2019 | Testers | Standard Specification for Gravity – Convection and Forced – Ventilation Ovens |
D5423 | 2023 | Insulation | Standard Specification for Forced – Convection Laboratory Ovens for Evaluation of Electrical Insulution | |
D5374 | 2012 | Insulation | Standard Specification for Forced – Convection Laboratory Ovens for Evaluation of Electrical Insulution | |
UL | 746B | 2013 | – | High polymer materials – Long-term property evaluation (Version 4) |
IEC | 60216-4-1 | Insulation | Electrical insulating materials – Thermal endurance properties – Part 4-1:Ageing ovens – Single – chamber ovens Reference |
Yasuda Seiki Tester: No.102, 103 Gear-type Aging Tester
Heat aging properties can be measured using the No. 102 Gear-type aging tester.
Related Products
Click here for inquiries
Yasuda Seiki’s testers, which have been supporting quality control and research and development in the industrial field for over 65 years, will fulfill the diverse needs of your company.
Reference Standards
- JIS B 7757 (1955) Forced circulation type air heating aging tester
- JIS K 6257 2017 Vulcanized rubber and thermoplastic rubber – Method to determine heat aging properties
- JIS K 7212 1999 Plastics – Thermal stability test method for thermoplastics – Oven method
- JIS C 3005 2014 Rubber/plastic insulated wire test method